Table of Contents
What is Container Plywood?
Understanding Container Floorboard
Container floorboards, typically made of plywood, play a crucial role in the structural integrity of shipping containers. These floorboards provide a sturdy surface for cargo, ensuring that goods are safely supported during transport. The importance of container plywood lies in its durability and ability to withstand various environmental factors, making it a vital component in the shipping industry.
Importance of Container Floorboards
- Provides a solid base for cargo, ensuring stability during transport.
- Contributes to the overall structural strength of the container.
- Helps protect the cargo from moisture and external elements by offering a durable, resilient surface.
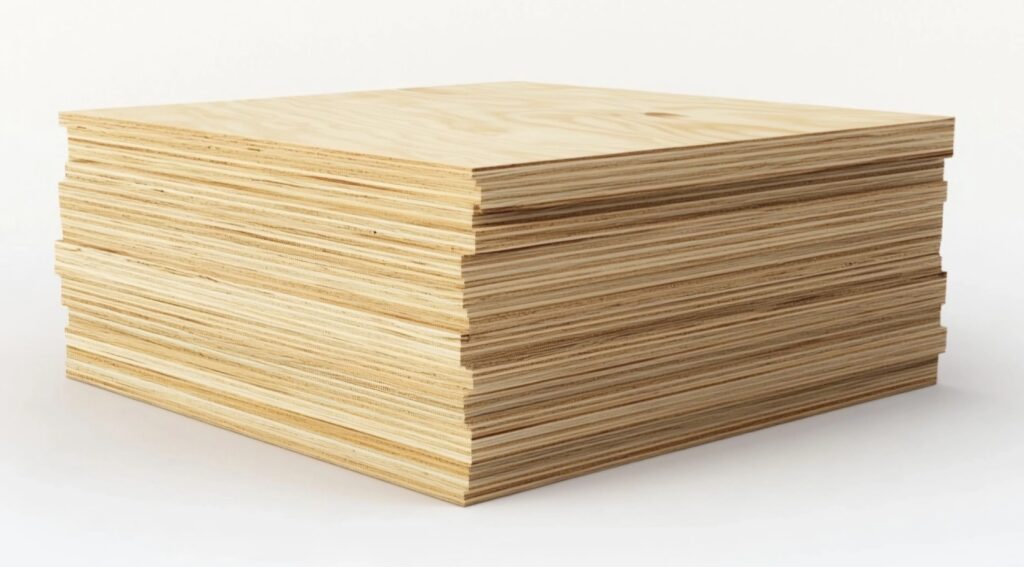
Types of Shipping Container Floorboard
The types of floorboards used in shipping containers vary based on the materials they are from and their specific applications. Below are the common types,
What are the Materials Used for Container Floorboards ?
Plywood: The most common material for container floorboards is plywood, which is known for its strength, durability, and resistance to warping. Plywood floorboards are typically made from hardwood species such as apitong or birch, which are chosen for their ability to withstand heavy loads and frequent use.
What are the Alternatives to Plywood ?
In some cases, alternatives like bamboo floorboards, steel, or composite materials are used. You can refer to the article Shipping Container Floorboards You Must Know, which discusses more than seven alternative floorboards.
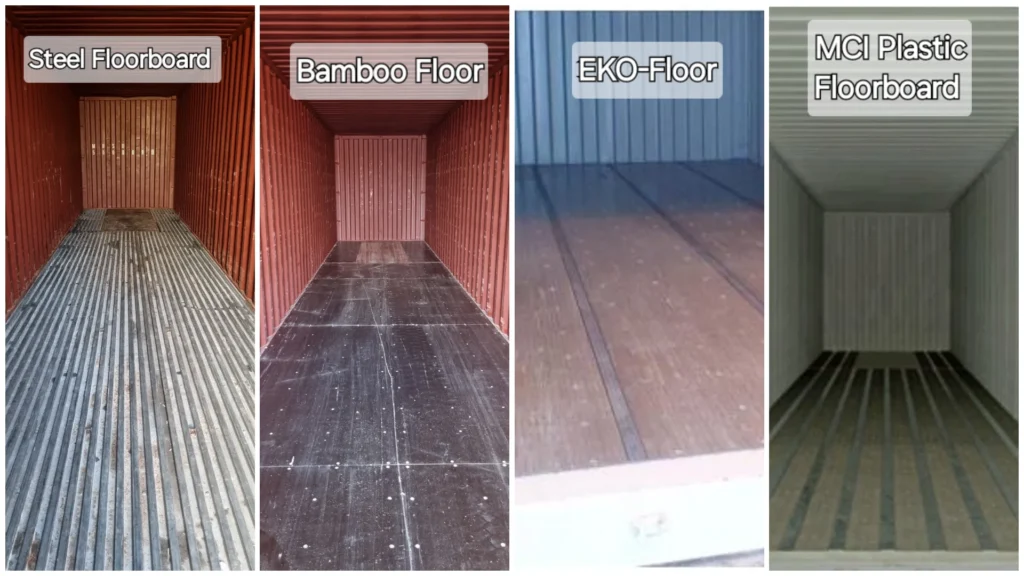
Shipping Container Floorboard Dimensions
Standard dimensions for shipping container floorboards are:
- Thickness: 28mm (1.1 inches)
- Width: 1160mm (45.67 inches)
- Length: 2400mm (94.488 inches)
Note: These dimensions can differ slightly based on the manufacturer or the type of container.
Ply count in Shipping Container Plywood ?
A shipping container floorboard usually has a minimum of 19 plies, ensuring it has the necessary strength and stability to withstand shipping and handling. The number of plies can go up to around 21, which can enhance durability and strength, though this may also lead to an increase in both weight and cost.
Note: The exact number of plies may vary depending on the manufacturer, the container’s intended use, and any extra requirements for strength or weight.
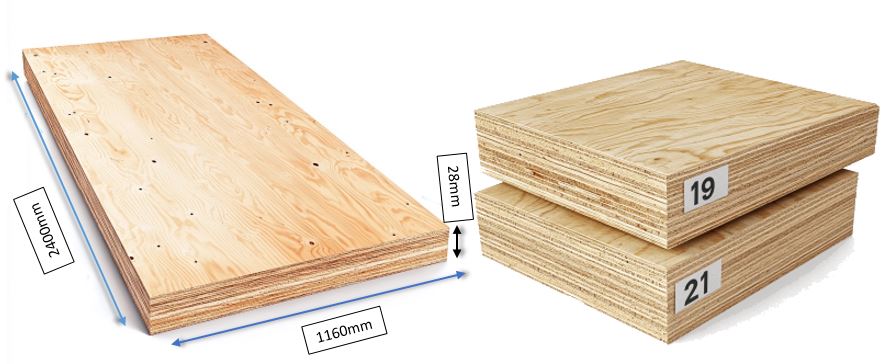
What is the ideal moisture content for container flooring ?
Moisture content in shipping container floorboards refers to the water present in the wood, usually expressed as a percentage of the wood’s dry weight. The typical moisture content for these floorboards ranges between 12% and 15%, which is generally acceptable for most applications. Maintaining a low moisture content is crucial for the durability and longevity of the floorboards. Proper drying techniques and storing the wood in a dry environment are essential to achieve this.
If the moisture content is too high, it can lead to several issues:
- Warping: Uneven drying can cause the wood to bend or twist.
- Mold and Mildew: Excess moisture creates a favorable environment for mold and mildew growth.
- Rot: Excessive moisture can lead to wood rot.
- Structural Integrity: High moisture content can compromise the floorboard’s structural integrity.
On the other hand, if the moisture content is too low, the wood may become more prone to cracking and splitting. Therefore, maintaining the appropriate moisture level is vital for the performance of shipping container floorboards.
Floorboard Installation Inside Shipping Containers
The floor of the container is supported by several key structural components, each playing a vital role in maintaining the integrity of the flooring. below components are directly involved in supporting the floorboards in a shipping container.
- Bottom side rails : These run along the length of the container, providing lateral support to the flooring.
- Crossmembers: Transverse beams that connect the bottom side rails, offering direct support to the floor.
- Outriggers: These structural elements are positioned on both sides of the tunnel plate and provide critical support to the floorboards.
- Forklift pockets (if any): Reinforced sections of the floor designed to accommodate the forks of a forklift.
- Center Rail (if present): In some container designs, especially those with higher load-bearing requirements, a center rail may be present. This rail runs along the center of the container floor and provides additional support to the floorboards, working alongside the crossmembers.
The floor itself is generally composed of plywood panels, although alternative flooring materials or steel may also be used. In some container designs, these plywood panels are further reinforced by a center rail that runs longitudinally down the middle of the container.
The section of the floor extending from the door sill to the first crossmember is often covered by a full-width Threshold (or crash) plate. This plate protects this part of the floor from damage caused by cargo handling equipment.
Floor Supporting Angles : These are L-shaped or angle sections, typically made of steel, that are attached to the sidewalls of the container. Their primary function is to provide additional support to the edges of the floorboards, helping to secure the floor to the container’s sidewalls and preventing any lateral movement. These angles work in conjunction with other structural components like the bottom side rails, crossmembers, and outriggers to ensure the floor remains stable and properly aligned within the container.
In a shipping container, floor supporting angles are typically located in the following areas:
- Along the Sidewalls: Floor supporting angles are installed where the floorboards meet the sidewalls of the container. These angles run parallel to the bottom side rails and help secure the floorboards to the sidewalls, providing lateral stability.
- At the Junction of the Crossmembers and Sidewalls: Floor supporting angles can also be found where the crossmembers connect to the sidewalls. These angles help distribute the load from the floorboards to the crossmembers and sidewalls, ensuring even support.
- Near the Door Sill: Supporting angles may be used near the door sill, where the floorboards meet the rear sill of the container. This placement helps reinforce the floor at the container’s entrance, which is a high-traffic area.
- Around the Tunnel Plate (if present): In containers with a gooseneck tunnel plate, supporting angles may be positioned where the floorboards transition to the tunnel plate, ensuring that the floorboards are securely attached around this area.
- Tunnel bolster : Floor supporting angles in this area are typically placed where the floorboards meet the . These angles help secure the floorboards to the tunnel bolster, providing additional stability and ensuring a smooth transition between the floorboards and the tunnel plate. This placement is crucial for maintaining the strength and integrity of the floor in the central part of the container.
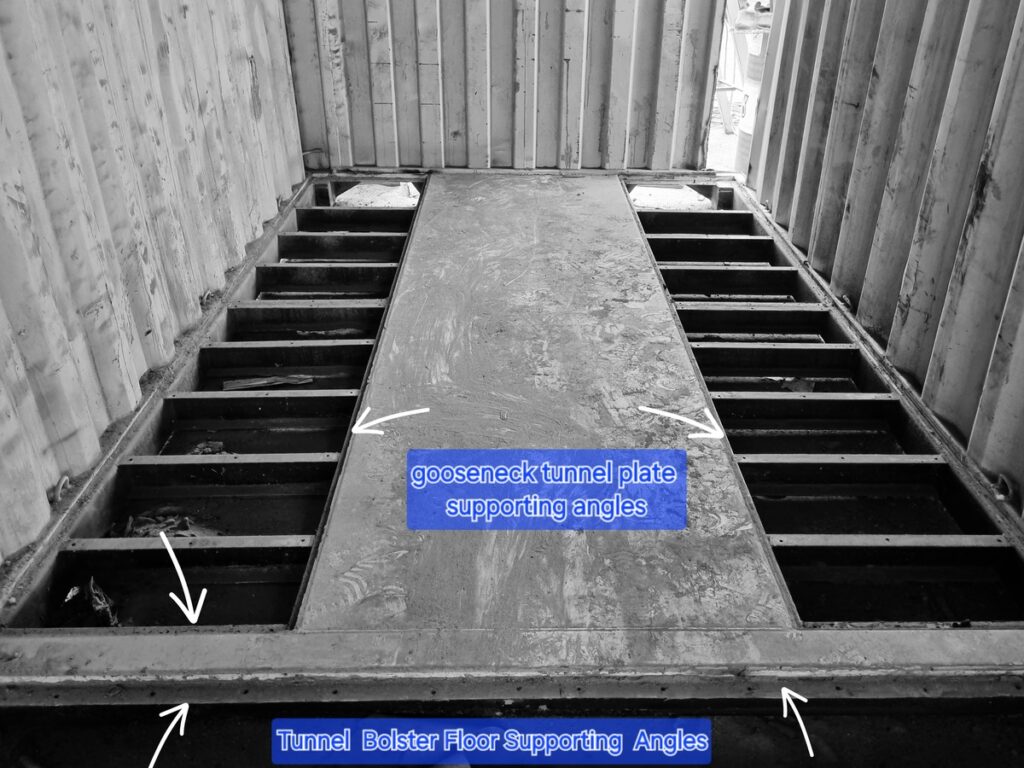
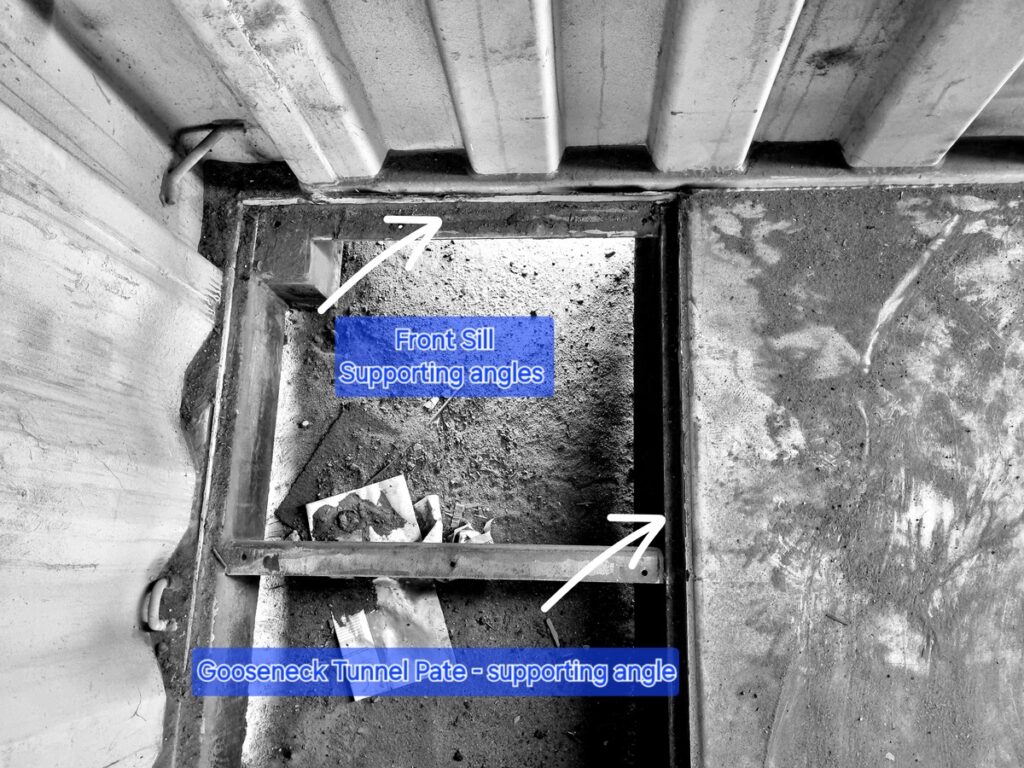
Floorboard Layout in a 40-foot & 20-foot Container
In a 40-foot shipping container, a total of 12 floorboards are installed. These include six boards measuring 2400x1160mm (8×4 feet), two boards that are typically 4×5 feet, and another four smaller pieces fitted over the outriggers on both sides of the tunnel plate.
From the rear sill to the tunnel bolster, you’ll find six long boards (8×4 feet) and two shorter boards (4×5 feet). The 4×5-foot boards are commonly referred to as “short boards,” while the 8×4-foot boards are called “long boards.”
Some containers have the first two floorboards near the rear as short boards, while others use long boards in that position. The two images below will help you understand this layout better.
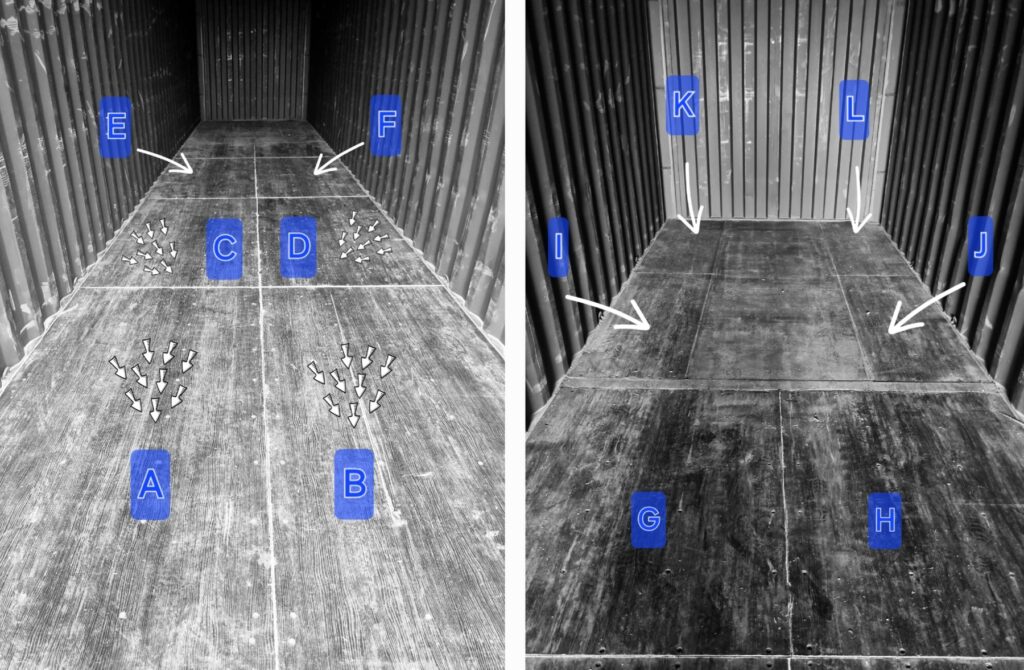
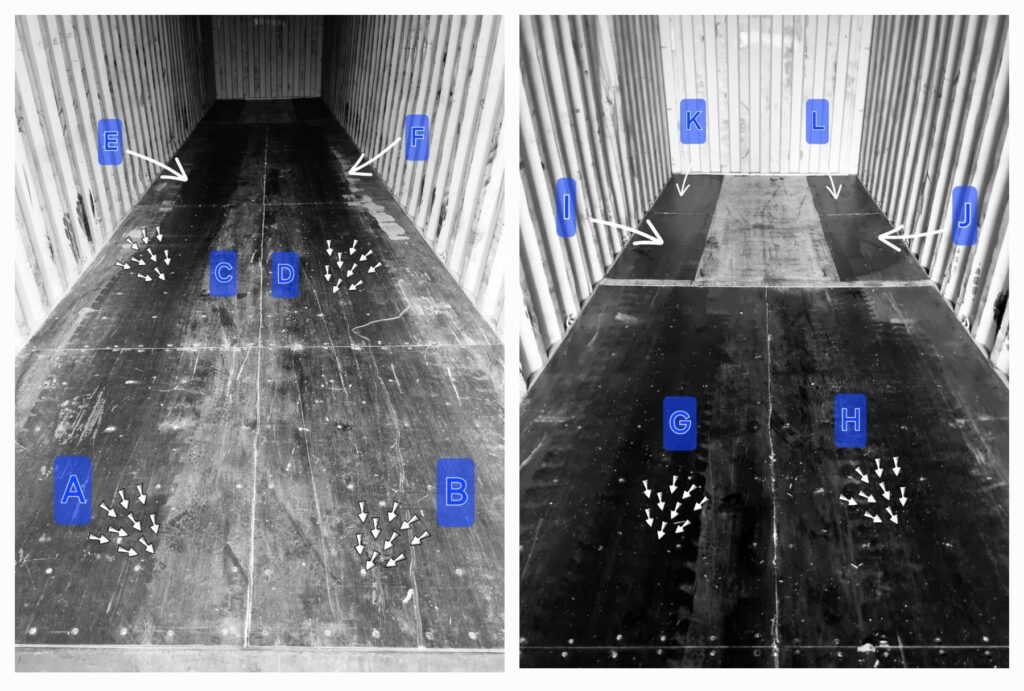
In a 20-foot shipping container, a total of 6 floorboards are installed. These include four boards measuring 2400x1160mm (8×4 feet), two boards that are typically 4×4 feet.
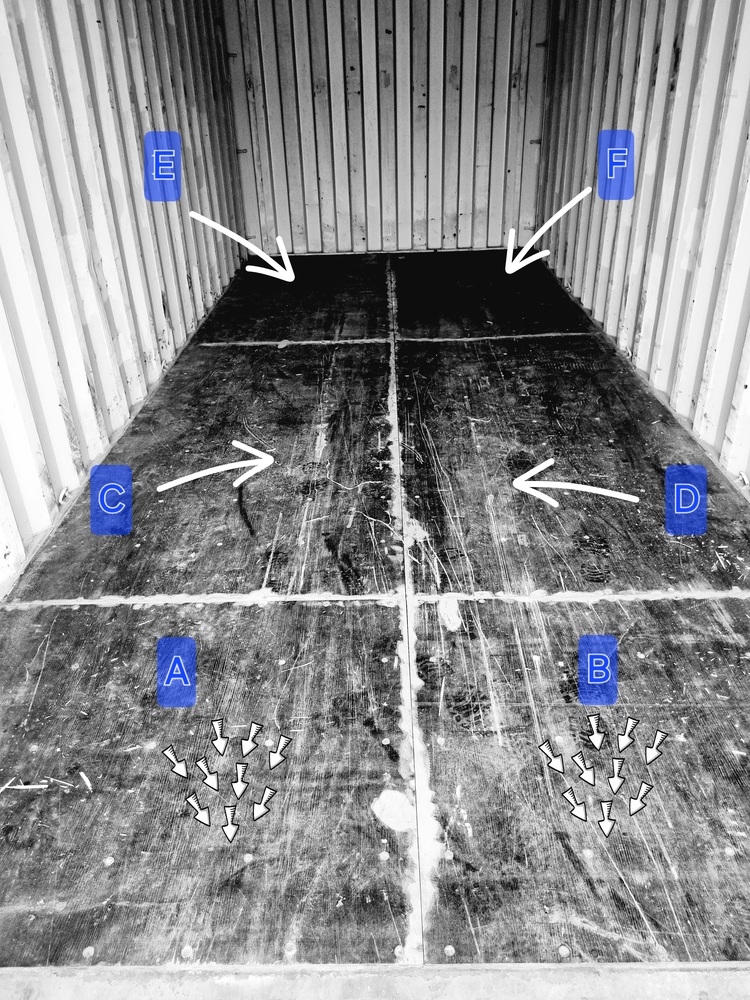
Screws Placement on Container Floorboards
The floor of a container is attached to the crossmembers using floor screws. Typically, 6 to 8 screws are used along each edge of the floorboard, while 4 to 6 screws are used on each crossmember. Additionally, 4 to 5 screws secure the floorboards to the edge of the outriggers, with 3 to 4 screws used in the middle of the floorboard to secure it to the outriggers.
Please note that these details may vary depending on the manufacturer, any repairs made after the container has been used, or specific requirements set by the container owner.
Coatings and Treatments for Container Floorboards
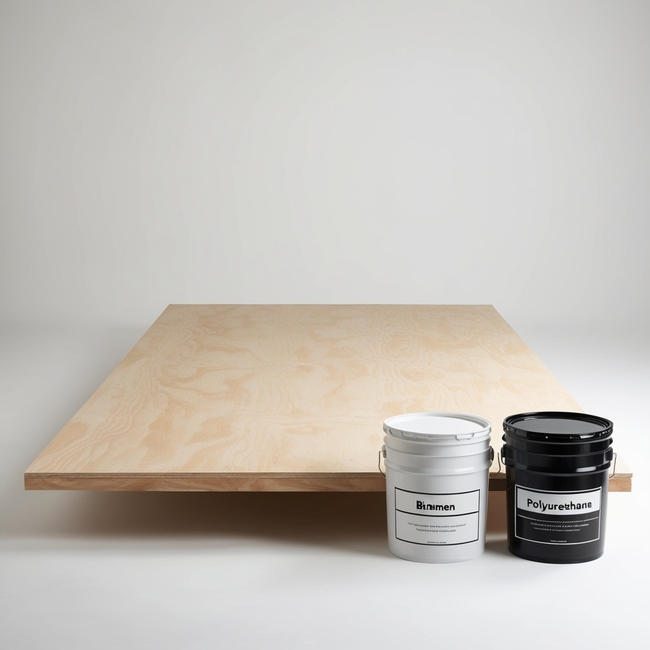
Enhancing the performance and longevity of container floorboards requires the application of proper coatings and treatments. These protective measures shield the floorboards from environmental challenges such as moisture, pests, and mechanical wear, ensuring the structural integrity and safety of the container.
Coatings
- Epoxy Coatings: Known for its exceptional durability, epoxy forms a robust barrier on container floorboards. Its resistance to chemicals and ability to withstand heavy loads make it ideal for industrial applications, where floorboards are exposed to harsh conditions.
- Polyurethane Coatings: Polyurethane offers superior abrasion resistance and UV protection. These qualities make it well-suited for outdoor container floorboards that face prolonged exposure to sunlight and weathering.
- Acrylic Coatings: While not as durable as epoxy or polyurethane, acrylic coatings provide effective moisture protection and environmental resistance. They are often chosen for their flexibility and cost-effectiveness, particularly in less demanding conditions.
- Bitumen Coatings: Bitumen is a highly effective moisture barrier, commonly used on the underside of container floorboards. Its water-resistant properties make it particularly useful in protecting the wood from prolonged exposure to wet conditions, thereby preventing rot and decay.
Treatments
- Pressure Treatment: To safeguard floorboards against decay, insects, and fungi, pressure treatment infuses the wood with preservatives. This treatment is crucial for extending the life of floorboards, especially in damp or pest-prone environments.
- Fire Retardant Treatments: In high-risk areas where fire safety is a concern, treating wood with fire retardants can significantly reduce flammability, adding a critical layer of protection.
- Anti-Slip Treatments: For enhanced safety in wet or oily conditions, anti-slip treatments create a textured surface on the floorboards, reducing the risk of slips and falls.
Manufacturer-Specified Coatings
When replacing container floorboards, it is essential to replicate the original manufacturer’s coatings. The new floorboards should be coated on both the underside and topside with the same material as the original—whether it be bitumen, polyurethane, or wax-based. If the original floor was primed, or if required by the container owner, a primer must be applied before the main coating. This step ensures proper adhesion and provides long-term protection.
By adhering to these practices, the floorboards are effectively shielded, preserving the container’s structural integrity and safety over time.
How to Check a Container Floor for Chemicals
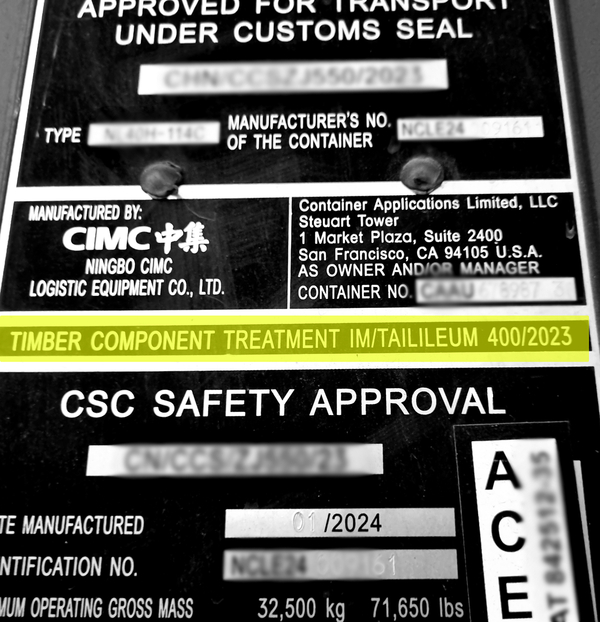
To check if the container floor has been treated with chemicals, inspect the Container Safety Convention (CSC) plate on the container’s front door. Look for the “timber component treatment” section, where you’ll find:
- Immunity (IM)
- Treatment chemical
- Treatment date
Focus on the treatment chemical and date to identify any pesticides used. You can refer to the World Health Organization’s guidelines to assess the safety of these chemicals. Be aware that this information might not always be accurate, as container floors are often replaced during maintenance.
Load-Bearing Capacity of Shipping Container Floorboards
Assessing the Load Capacity of Shipping Container Floorboards
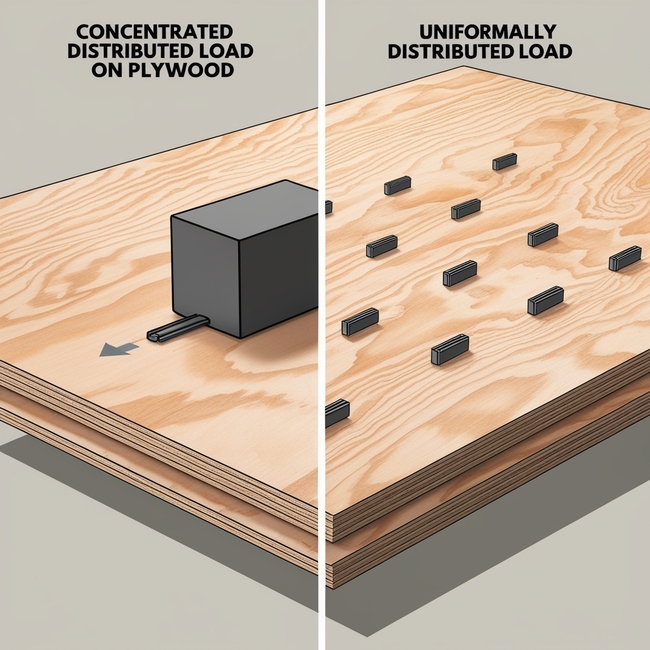
When determining how much weight a shipping container floorboard can handle, it’s essential to consider both the Uniformly Distributed Load (UDL) and Concentrated Load capacities. These measurements provide insights into the floorboard’s ability to support different types of loads.
When determining how much weight a shipping container floorboard can handle, it’s essential to consider both the Uniformly Distributed Load (UDL) and Concentrated Load capacities. These measurements provide insights into the floorboard’s ability to support different types of loads.
Uniformly Distributed Load (UDL)
Capacity: Typically, floorboards in shipping containers are designed to support a UDL of approximately 5.46 metric tons per square meter (about 560 kg per square foot).
Factors Influencing UDL: This capacity can vary depending on the floorboard’s material, thickness, and the overall design of the container. Plywood floorboards, for example, generally meet this standard, but the specific load capacity may change with the use of different materials or construction techniques.
Concentrated Load
Capacity: A common figure for concentrated load capacity is 726 kg (1,600 lbs). This applies to situations where a heavy load is applied to a small area of the floor, such as under the wheel of a forklift.
Risks: It’s important to note that concentrated loads can cause significant damage if they are not distributed evenly or if they are applied near the edges of the container floor. Overloading in these areas can lead to floorboard failure.
Key Factors Affecting Load Capacity
- Floorboard Material: Plywood and steel are the most common materials. Plywood is generally less robust than steel, but with proper use, both can handle substantial loads.
- Floorboard Thickness: Thicker floorboards can naturally support heavier loads, making this an important consideration in load capacity assessment.
- Container Design: Some shipping containers are built with reinforced floors, enabling them to handle greater weights.
- Weight Distribution: Properly distributing weight across the entire floorboard surface is crucial. Uneven distribution can lead to localized damage and potential failure.
Shipping Container Floorboard Testing Requirements
For container floorboards to meet industry standards, they must undergo and pass several rigorous tests to ensure durability and performance:
IICL Short Span Test: As per the IICL Performance Standard for Plywood Floor Panels (IICL TB001, section 3.1), this test assesses the strength of the floorboard over a short span, simulating real-world loading conditions.
Bending Strength and Elastic Modulus: This test, detailed in section 4.9 of the GB/T 19536-2004 standard, measures the floorboard’s ability to withstand bending forces and its elasticity under stress.
Boiling Test: Also under the GB/T 19536-2004 standard, the boiling test evaluates the floorboard’s resistance to moisture by subjecting it to extreme boiling conditions.
ISO 1496 Floor Strength Test: This test requires the floorboard to withstand a truck load of 7,260 kg, ensuring it meets the strength requirements for shipping containers.
COA Short span floor test : This technical document describes a short-span test procedure designed to be undertaken by the service- provider within the depot.
Organization involvement for Shipping Container Floorboard
Australian Quarantine and Inspection Service (AQIS) Involvement in Container Plywood
The Australian Quarantine and Inspection Service (AQIS) is a key organization responsible for enforcing biosecurity standards in Australia. AQIS requires that container plywood be treated to prevent the introduction of pests and diseases. This involves specific chemical treatments or fumigation, ensuring that all imported containers meet Australia’s stringent biosecurity regulations. AQIS’s involvement is crucial in protecting the country’s agricultural and natural environments from invasive species.
Forest Stewardship Council’s Role in Container Plywood
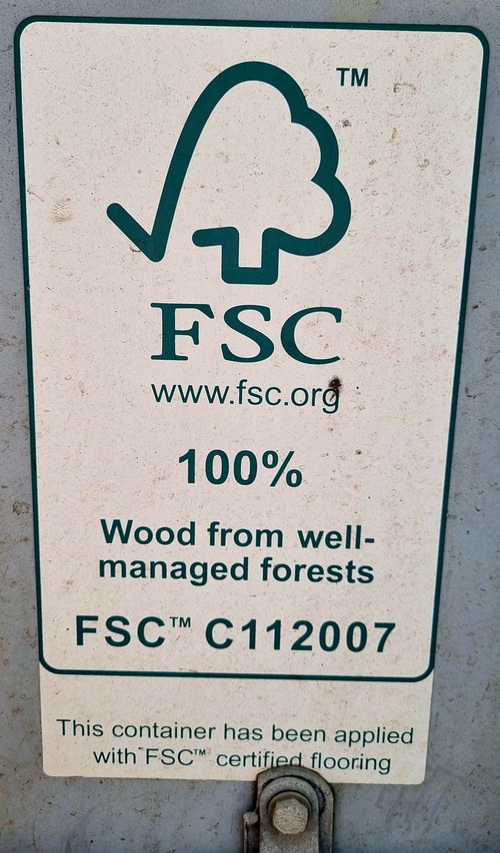
The Forest Stewardship Council (FSC) is an international organization that promotes responsible management of the world’s forests. FSC certification is essential for container plywood, ensuring that the wood used is sourced from sustainably managed forests. This certification reflects the organization’s commitment to environmental protection, social responsibility, and economic viability. By adhering to FSC standards, companies involved in container manufacturing contribute to the preservation of forests and the well-being of communities dependent on them.
Common Causes of Floorboard Damage
Shipping container floorboard damage typically occurs due to moisture exposure, overloading, and improper handling. Moisture can weaken the plywood, causing warping and rot, while overloading beyond the container’s weight limits can lead to cracks or breakage. Additionally, forklifts and heavy equipment inside containers can exert excessive pressure on weak points, further damaging the floorboards. Regular inspection and proper loading practices are essential to prevent such issues.
Check the article of 18 Effective Methods for Identifying Container Floor Damage
How to fix Shipping Container Damage Floor
There are different ways to repair shipping container floorboard and methods as follows,
- Floor cleaning
- Dowel Repairs
- Floorboard Sectioning
- Complete floorboard Replacing
- Floor screws replace or refit
- Floor Power Grinding or Sanding