Table of Contents
Shipping Container Plywood
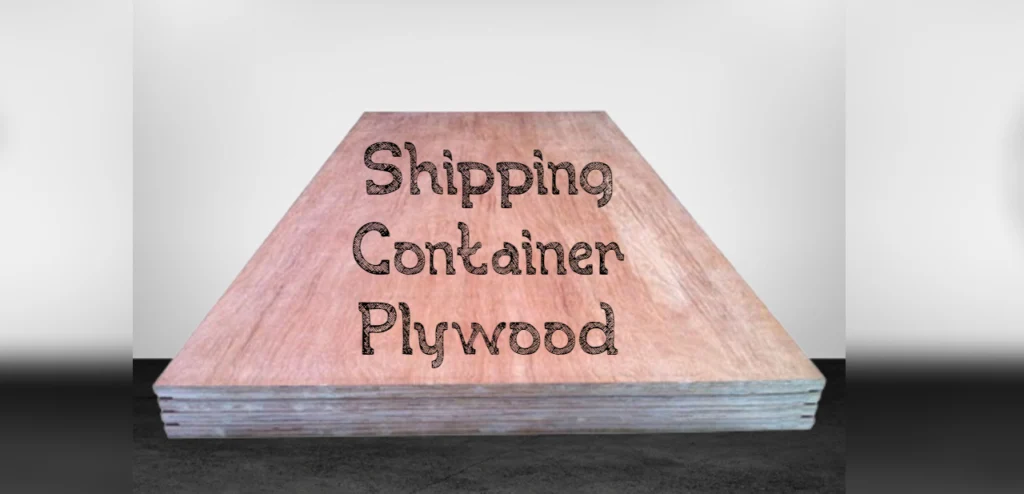
Shipping container floorboard, also known as container flooring, is an engineered structural material made from layers of wood veneer of varying thicknesses, glued or bonded together. The wood grains in each layer are arranged at right angles or parallel to each other. This construction method gives the floorboard significant strength and durability, essential for the tough conditions faced by shipping containers.
This floorboard is a vital part of the container’s durability and functionality, especially given its role in transporting and storing goods. Its robust design ensures it can handle heavy loads and endure constant wear and tear during transit.
Shipping container standard floorboards are typically made from high quality tropical hardwoods species such as Apitong(Keruing), Brich, Maple or Oak.
What is shipping container softwood Floorboard ?
Softwood plywood is less common for container flooring due to its lower strength and durability compared to hardwood and common spices are Pine, Fir and Spruce.
Steps Involved in the Shipping Container Plywood Manufacturing Process
Selection of a Log
A suitable log, called a “peeler,” is chosen for its straightness and adequate diameter to produce multiple layers. Logs are transported to the mill for processing.
Debarking
Logs are placed on a chain conveyor and transported to debarking equipment, which removes the bark using high-pressure water jets or grinding wheels. The debarked logs are then cut into pieces.
Cutting the Logs
Debarked logs are cut to the required size, ensuring quality and consistency in the finished product.
Peeling the Logs
Logs are peeled using a rotary lathe, producing long veneer sheets. These sheets can be machined immediately, stored, or rolled up.
Grading and Sizing
Veneer sheets are sized to a standard 4′ x 8′ and scanned for quality. The sheets are then stacked and transferred to drying ovens.
Glue Application
Veneer sheets are assembled and coated with glue, either manually or by machine. The rear veneer runs through a glue spreader to ensure an even coating.
Pressing
Pressing occurs in two stages: cold pressing flattens the veneers and ensures even glue application, while hot pressing applies heat and pressure to bond the veneers firmly.
Sanding, Trimming, and Finishing
Boards are sanded, trimmed, and finished to remove any imperfections, ensuring square edges and a smooth surface.
Quality Control
Quality control tests, including moisture content and durability assessments, are conducted throughout the production process to ensure the final product meets standards.
Pros and Cons of Shipping Container Bamboo Floorboard
Pros | Cons |
---|---|
Strength & Durability – able to withstand heavy loads and rough usage. | Moisture Sensitivity – Susceptible to moisture and can rot or wrap if not properly treated and maintained. |
Repairability – wooden floorboards can be repaired. | Pest Vulnerability – Can be prone to infestations by pests such as termites or beetles. |
Insulation – provides natural insulation properties, helping to maintain temperature stability inside the container. | Fire Risk – wood is flammable and can pose a fire hazard. |
Versatility – Plywood can be cut and shaped to fit various container sizes. | Chemical Sensitivity – certain chemical or spills can damage wooden floorboards. |
Cost – Generally more affordable than some alternative materials. | Limited Lifespan – Compared to alternative flooring options, wood may have a shorter lifespan. |
Shipping Container Bamboo Plywood
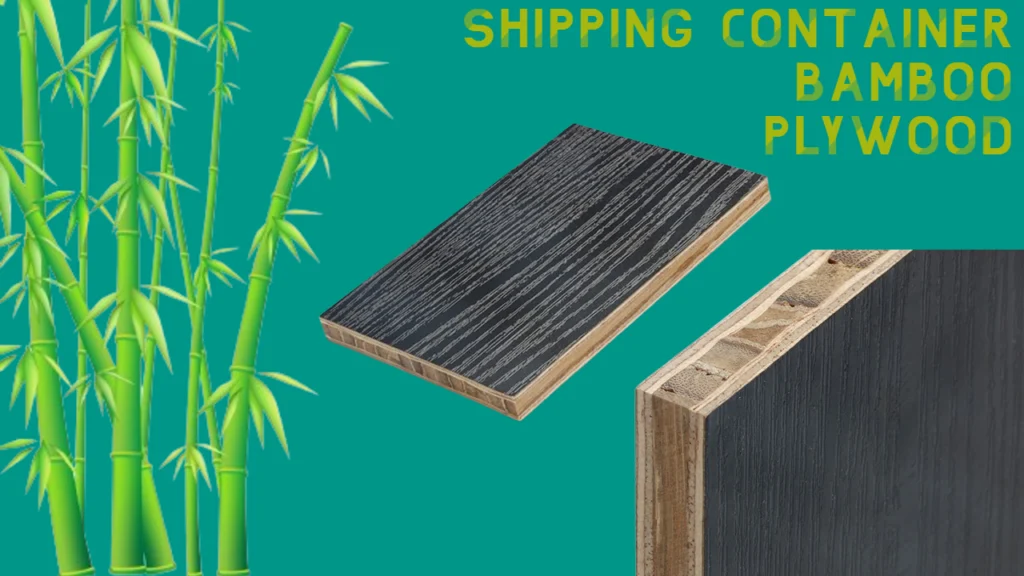
Bamboo floorboard refers to a type of flooring material made from 100% Bamboo Plant. And typically made by laminating several layers of bamboo strips or fibers. This is eco-friendly and low maintenance required comparing to standard shipping container plywood.
Bamboo Plywood Manufacturing Process
Here is a general overview of the bamboo plywood manufacturing process.
Harvesting: Bamboo is sustainably harvested and then cut into long strips.
Slicing: These strips are sliced into thin sheets or “veneers” using a veneer slicer. The thickness of these veneers varies based on the desired thickness of the final plywood.
Boiling and Drying: The veneers are either boiled in water or soaked in a chemical solution to eliminate impurities and enhance durability. They are then dried to lower their moisture content.
Gluing: Adhesive is applied to the veneers, which are then stacked in alternating grain patterns. The adhesive used is typically a waterproof, formaldehyde-free resin to ensure a strong, durable bond.
Pressing: The glued veneers are placed in a hot press and compressed under high pressure and temperature, forming a solid, uniform panel.
Finishing: The bamboo plywood is sanded, trimmed, and may receive a protective coating or stain to improve its durability and appearance.
Pros of Shipping Container Bamboo Floorboard
High Hardness – bamboo plywood is exceptionally hard and resistant to wear and tear.
Structural Stability – offers excellent structural stability, ensuring that the floorboards remain strong and intact even under heavy load.
Better Moisture Handling – treated bamboo plywood can handle moisture better than many other types of wood.
Ease of Maintenance – relatively easy to maintain, requiring only simple cleaning and occasional protective treatments to keep it in good condition.
Cost-Effective – more affordable than traditional hardwoods
Because of these advantages, most shipping lines, leasing companies and container manufacturers are now using bamboo plywood.
Bamboo OSB (Oriented Strand Board)
Bamboo OSB is an innovative and eco-friendly building material made entirely from the fast-growing bamboo plant. This composite board is engineered by layering strands of bamboo in specific orientations and bonding them together with high-strength MDI (methylene diphenyl diisocyanate) adhesives under heat and pressure.
Bamboo Hardwood
The engineered hardwood features 23-layers with 17 layers of bamboo and 6 layers of domestic eucalyptus wood.
Bamboo-Pine Composite
This innovative plywood is composed of a blend of 70% bamboo and 30% pine/eucalyptus. There are 22 plies of pine and bamboo curtain sealed with a varnish on a paper finished.
Bamboo Hybrid
Eco-Friendly plywood composed 21 plies ( Bamboo curtain 9 plies and wood veneers 12 plies )
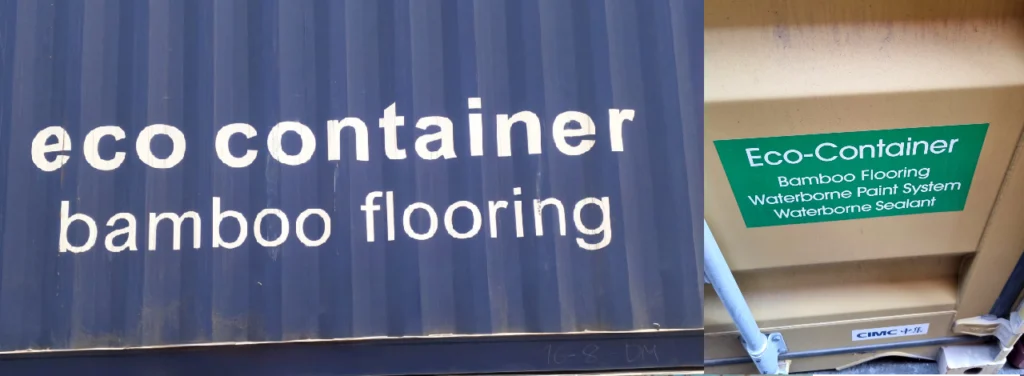
Shipping Container Steel Floorboard
A shipping container steel flooring is the sturdy metal base you can find inside standard shipping containers. It’s made from corrugated steel sheets that are welded together. also can be identified as one of the alternative floor materials and designed to transport all cargo. This floor is built to handle heavy loads endure the rigors of loading, unloading and various environmental conditions.
The floor is composed of five 8-foot-wide by 4-foot-long steel sheets with longitudinally oriented stamped corrugations that enhance strength and enable the thickness to be lowered to just 3.2 mm.
Pros and Cons of Shipping Container Steel Floorboard
Pros | Cons |
---|---|
Durability: Steel floorboards are more durable compared to traditional materials, making them ideal for the rough conditions faced by shipping containers. | Higher Manufacturing Cost: The initial cost of manufacturing steel floorboards is higher compared to traditional materials. |
Reduced Repairs: Due to their durability, steel floorboards require fewer repairs over their lifespan. | Non-Nailable: Steel floorboards cannot be nailed, which may complicate installation and modifications. |
No Delamination: Steel floorboards do not delaminate, ensuring a consistent and reliable flooring surface. | Potential Corrosion Issues: Steel is susceptible to corrosion, especially in harsh or humid environments, which can compromise its integrity over time. |
Eco-Friendly and Recyclable: Steel floorboards are 100% recyclable and considered eco-friendly, contributing to environmental sustainability. | Higher Tare Weight: Steel floorboards add more weight to the container, potentially affecting shipping costs and handling. |
No Special Disposal Needed: Unlike some materials, steel does not require special disposal methods, making it easier and cheaper to handle at the end of its life. | High Repair Costs: When repairs are needed, the cost can be higher due to the material and specialized skills required for fixing steel. |
Hygienic: Steel floorboards are odorless, resistant to humidity, and do not require chemical treatments, making them more hygienic and easier to clean. | Thermal Conductivity: Steel can conduct heat, which may lead to temperature variations inside the container, affecting stored goods. |
Hapag Lloyd Steel Floor Container
Shipping Container Hybrid Plywood
Hybrid plywood for shipping containers is a type of plywood designed to enhance performance by combining different materials. It typically has a core made of traditional wood layers, which are then combined with other materials like steel or fiberglass. This combination improves the plywood’s strength, durability, and resistance to environmental factors.
Larch/Brich hybrid Plywood
This plywood is made up of 21 layers of veneers and features a phenolic coating on its top surface. The core consists of a mix of brick and larch veneers, providing a sturdy and durable structure.
Shipping Container Composite Plywood
Composite plywood for shipping containers is made by bonding layers of wood veneer with other composite materials such as resin, plastic, or synthetic fibers. These composites are designed to improve specific properties like durability, moisture resistance, and structural strength.
FRP Composite Floorboard
Fiber Reinforced Polymer (FRP) composite floorboards are making waves in the shipping industry, FRP composite floorboards are made by combining a polymer (like resin) with reinforced fibers (such as glass, carbon, or aramid). This combination creates a material that’s used as flooring in shipping containers.
Key Features of FRP Composite Floorboards
Durable: These floorboards are designed to handle heavy loads and resist wear and tear, making them suitable for the constant loading and unloading in shipping containers.
Corrosion-Resistant: Unlike traditional materials like wood and steel, FRP composites don’t corrode or rot when exposed to moisture or harsh conditions. This is crucial for shipping containers that often encounter salty sea air and varying climates.
Lightweight: FRP floorboards are lighter than many traditional materials, which can help reduce the overall weight of the container. This can be beneficial for shipping efficiency.
Low Maintenance: Once installed, FRP composite floorboards require minimal upkeep compared to wood or steel, which can save time and money in the long run.
WPC Composite Floorboard
If you’re looking to upgrade the flooring in your shipping containers, Wood Plastic Composite (WPC) floorboards might be just what you need.
WPC composite floorboards are made by combining wood fibers with plastic. This combination creates a material that incorporates the best qualities of both components, resulting in a durable and versatile flooring option. They offer a practical and sustainable solution for shipping container flooring.
These floorboards combine the best features of wood and plastic, providing durability, moisture resistance, and low maintenance. While they may have a higher initial cost and require specific installation methods, their long-term benefits make them a viable option for those looking to enhance the functionality and appearance of their shipping containers.
In short, WPC composite floorboards are a smart investment for anyone needing reliable and sustainable flooring for shipping containers.
Differences Between Hybrid Plywood and Composite Plywood
Material Composition: Hybrid plywood is a mix of traditional wood veneers and other materials like steel, fiberglass, or bamboo. This combination keeps a lot of wood content but adds these other materials to boost strength and durability. Composite plywood, however, is made by bonding wood veneers with materials like resin, plastic, or synthetic fibers. The goal here is to blend wood with non-wood materials to create a stronger, unified composite.
Primary Use and Benefits: Hybrid plywood is designed to bring together the best features of wood and other materials. It’s perfect for situations where you need extra structural strength, durability, and resistance to environmental factors. Composite plywood, on the other hand, is all about enhancing specific properties like moisture resistance, chemical resistance, and overall durability. This makes it great for environments where regular wood wouldn’t last long.
Manufacturing Process: Making hybrid plywood involves layering wood veneers with materials like metal or fiberglass, which often requires special bonding techniques. For composite plywood, the process involves impregnating wood veneers with synthetic resins or blending wood fibers with plastic or other composites.
Environmental Impact: Hybrid plywood can be more eco-friendly since it often uses renewable materials like bamboo along with traditional wood. Composite plywood, while very durable and low-maintenance, usually relies on synthetic materials, which might not be as environmentally friendly.
Shipping Container Plastic Floor
Shipping containers often use different materials for their floors, like steel, plywood, bamboo, or plastic. Plastic floorboards, usually made from tough, high-density polyethylene (HDPE) or recycled plastics, offer several great benefits.
- Durability: They stand up well to moisture, chemicals, and pests, making them very long-lasting.
- Eco-Friendly: Since they’re often made from recycled materials, they help support sustainability efforts.
- Low Maintenance: They’re easier to clean and maintain compared to traditional wood floors.
- Lightweight: Being lighter than wood floors, they can help reduce shipping costs.
- Safety: They often come with a non-slip surface, which provides better traction and safety.
“MCI” Plastic Floorboard
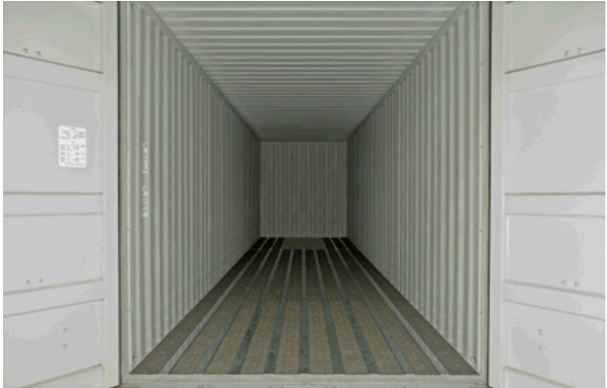
The MCI floorboard, designed by Maersk Container Industries (MCI) for Maersk, is an innovative flooring solution made from recycled plastics such as old plastic bags, milk bottles, and food wrappings, combined with steel omega sections for added strength. This eco-friendly design incorporates 10 recycled plastic planks interspersed with 9 steel omega sections across the width of a container. Unlike the Eko-Flor, which uses high-grade plastic to eliminate the need for steel reinforcement, the MCI floorboard emphasizes sustainability by repurposing low-grade plastics. Despite its environmental benefits, the production of the MCI floorboard was discontinued due to higher costs compared to bamboo alternatives.
EKO-FLOR Plastic Floorboard
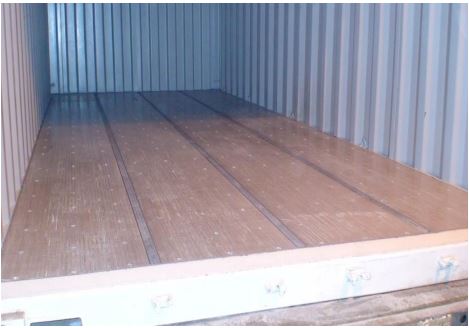
Eko-Flor is an advanced flooring solution designed for shipping containers that offers numerous benefits over traditional materials. This innovative flooring is known for its durability and resistance to moisture, making it a reliable choice for various demanding applications. Initially, Eko-Flor planks measured 547mm in width and required steel spacers for installation. However, the new and improved design features wider planks at 580mm with rubber seals, eliminating the need for spacers and providing a more seamless fit. Remarkably lightweight, Eko-Flor is about 23% lighter than tropical hardwood plywood, yet it still meets or exceeds the strength characteristics of wood. Made from abundantly available mineral-based materials, it is both reusable and recyclable, promoting sustainability. Additionally, Eko-Flor is easy to clean and doesn’t need a protective coating on the underside, simplifying maintenance. Whether used in new constructions or for repairs, Eko-Flor’s combination of strength, sustainability, and ease of installation makes it an excellent choice for modern flooring needs.
Marine Grade Plywood / Marine Plywood
Marine grade plywood is built to endure harsh environments, particularly those with constant or elevated moisture levels. Manufactured to the highest standards, this plywood is made from high-quality, defect-free veneers and uses waterproof adhesives. This construction ensures it remains strong and stable even when exposed to water for extended periods. Because of its durability, marine grade plywood is commonly used in boat building, docks, and other areas where long-term exposure to moisture is a concern.